A day in the life of an avionics repair technician
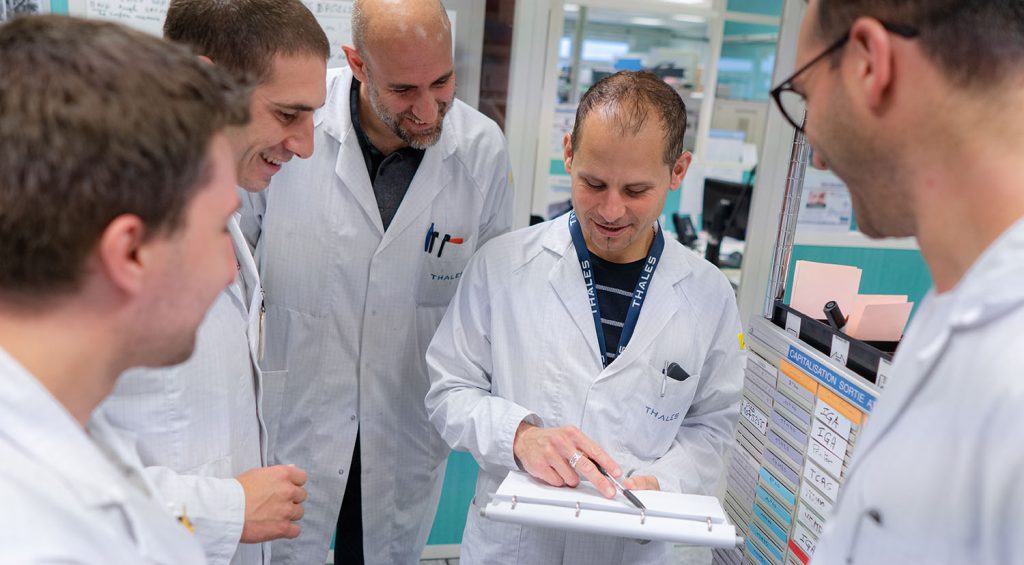
Could you tell us about your profession and your career?
I am currently involved in the repair of avionics equipment mounted on helicopters. On a daily basis, my job is to search for failures, coordinate repairs and ensure that the equipment entrusted to us by our clients (helicopter operators) is put back into service.
After my diploma in electronics obtained in 2002, I started at Thales on the Customer Support Center in Châtellerault (CSC), central France, first on an interim basis and then on a permanent basis. As an enthusiast of aeronautics, electronics and complex technology, the choice to steer my career towards Thales was obvious.
I started my career in retrofit; my role was to modify on-board computer equipment. Then, little by little, thanks to my own curiosity and proactivity, I was entrusted with increasingly complex equipment that was integrated in linefit installations and required a great deal of expertise.
Today, I am in charge of repairing the displays installed in the cockpit. These screens display data to help the helicopter pilot know the current state of the aircraft, giving information such as engine parameters, temperature, fuel level, etc. Also, because of my expertise, I exchange with the Product Support Engineers on all the technical aspects of the equipment I repair. We discuss problems encountered in production or repair, and the potential improvements to be made, and so on.
And finally, I have the role of coach for newcomers, which is particularly close to my heart. This role involves training young people in this profession and making sure that they feel welcomed under the best conditions to gradually learn to master the technicality and complexity of our equipment.
What are the necessary skills in your work?
We have a big responsibility, because the equipment has to work perfectly on the aircraft. There is no margin for error and we must provide constantly high quality work while respecting turnaround time (TAT) constraints to return the equipment to the customer.
I check the repair steps several times, I make sure the repair is conducted perfectly and in total respect of the processes set by the regulations in force and the technical documentation.
I am also interested in learning how to repair new equipment and about more efficient repair techniques.
So to summarize, I would say being responsible, meticulous and curious are key qualities for a repair technician. Then, I would add that it is essential to love teamwork and to listen to others.
In short, how does the repair of avionics equipment go?
On receiving defective equipment, its path and follow-up are optimized thanks to our internal processes and visual management. We use the latest technologies and methodologies to optimize our entire organization.
To begin with, I conduct the first tests to confirm the origin of the failure indicated by our client. These tests are carried out on specific test benches: the equipment is switched on and the electronic functions checked. Following the analysis of the breakdown, I make a preliminary report on the interventions: I estimate the recommended time and repairs that will then be quantified by our customer relationship service.
Following acceptance of the quotation by the customer, I start my repair work, thanks to the technical documentation and I order the replacement parts from our internal store, on site. Once the components are delivered, the electronic circuit passes through the expert hands of my colleagues in wiring who weld the components together. Then I take care of the final assembly before testing the equipment to verify the success of the repair.
Finally, I proceed to Release Approval which is the last line of defense to verify the quality of the repair before sending the equipment to the customer to be mounted in a helicopter. I make sure that everything was done properly and that the customer order was respected.
And finally, a few words about the CSC site?
Overall the atmosphere on the site is friendly and despite its size, we all know each other more or less. The working atmosphere within my team is very cordial and supportive. We have a lot of autonomy in our work, but always work as a close-knit team; it’s nice to be able to count on each other!