Customer satisfaction is everybody’s business
Coinciding with national Lean Processes day in France on 29 September, OnBoard spoke to Jean-Philippe Delval, Lean Supply Chain Manager for Thales’s avionics business, to find out more about these concepts and how they are changing the way Thales works.
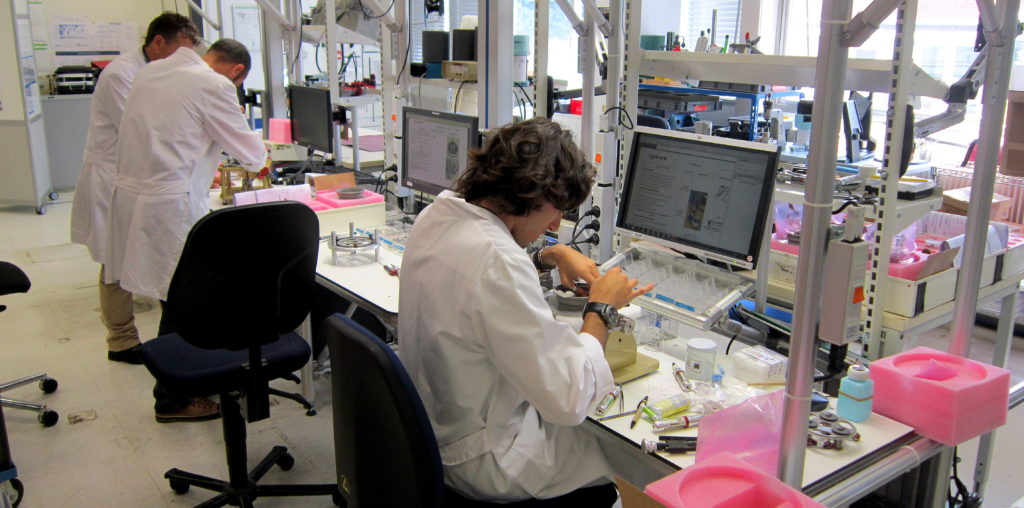
It started in the automotive industry with Toyota, then spread to other sectors. In the aerospace industry, aircraft manufacturers started the ball rolling and encouraged their equipment suppliers to follow suit. The original goal was to optimise production processes to maximise customer satisfaction — and that’s still the case today. But nowadays Lean is part of a continuous improvement process involving stakeholders at every level of the supply chain.
How has Thales introduced the Lean approach?
The impetus came from our customers. They had benchmarked their processes against those in place in the automotive industry, and found there were significant opportunities for raising production rates without permanently straining the system. At Thales, we started at the local level with a project on a single manufacturing line, then progressively deployed the concept throughout the Group. Today we apply the Lean approach not only to production and production support but also, increasingly, to product development.
When did you reach a tipping point?
When we stopped focusing on process improvements for individual activities and started thinking in terms of just-in-time everything for the overall system. That shift in focus has allowed us to structure all our activities around a single, clearly defined goal.
How has the workforce responded?
People have welcomed the new approach because they have received the support they needed at every stage. We put in place a comprehensive support system starting with the Industrial Director and extending down to local management. We coached managers individually and then it was up to them to coach their teams and make sure everybody was on board with the ideas and understood the details.
Which activities have been affected the most?
Production and production support — in other words all our industrial activities — have definitely been the most impacted. This is where we have achieved the highest level of lean process maturity. But today we are introducing the Lean approach in areas well beyond the scope of production and production support, and in product development and engineering in particular. We are also in constant contact with our suppliers and customers to share our latest practices as much as possible.
What measurable results have you achieved?
Performance has improved in many ways. One example is our inventory management system, which we have completely overhauled. At each stage in the production process, inventory now stays at the supplier’s premises until the customer needs it, so the supplier has a better perception of the customer’s production flows. Another concrete example is the way non-compliances are handled. Today the production support team comes and analyses the problem and takes the measures needed to deal with the non-compliance at the operator’s workstation, so that problems can be resolved quickly and efficiently.
What’s next on the Lean agenda?
We will be building on the achievements in lean production to adopt the approach more widely. Other sectors such as engineering are already introducing lean processes. Of course we won’t be replicating exactly what we did in production, but rather adapting the same methods to meet a different set of requirements. The support functions will follow.
-------------------------------------------------------------------------------------------------------------
The Thales approach to Lean
Lean is above all a model of management based on developing each individual’s contribution to team performance, and ultimately to customer satisfaction. The success of a Lean approach hinges on hands-on management involvement on the ground, a shared vision of the team’s goals and objectives, and individual empowerment so that each team member can make their jobs more relevant and rewarding by improving their problem-solving abilities.
Deploying a Lean approach relies on unequivocal engagement by senior management to provide a clear vision and shared direction, maintain a strong local presence on the ground, and support teamwork at every stage in the process.
Find us on Twitter @thales_avionics, on our official Youtube channel Onboard TV and on LinkedIn Thales Aerospace.