Optimizing the Thales supply chain for improved responsiveness
Since 2009, Thales has been gradually rolling out a large-scale initiative aimed at optimizing its worldwide maintenance and service supply chain. The project, called WINGS (Worldwide Integrated New Global Services), focuses on streamlining flows and processes in order to improve response time vis-à-vis customers.
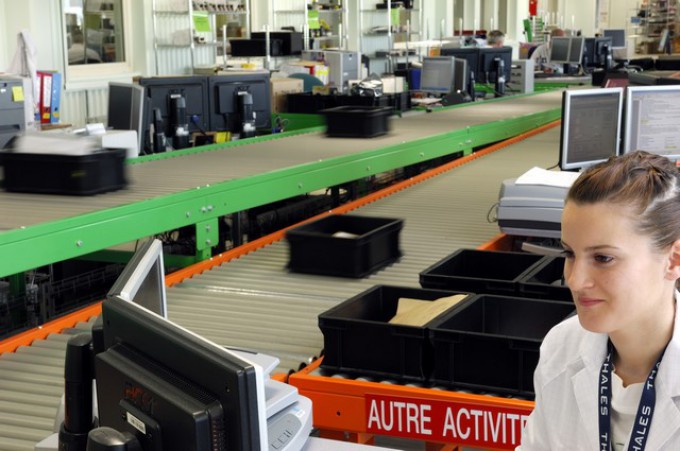
One of the main changes is a shift to a direct shipment approach, aimed at reducing transit time. Patrice Daret, who has lead on the WINGS project, explains that this switch is the result of a thorough Lean analysis: “Now, avionics parts and products are delivered directly from Thales premises to our customers without any superfluous and time-consuming logistical stops within the Thales supply chain.”
The shipment process originates from regional stocks located near the supplier and flows directly to the customer. Customers operating in a region far from Thales suppliers will benefit from improved transit times, which in turn have a positive impact on on-time delivery to the clients.
Fast returns
The newly-simplified shipment process has quickly delivered results. At the end of 2011, just a few months after the implementation of the new system, the number of internal stops had been almost halved, “a major result” according to Patrice Daret.
Another change has been the roll-out of a “push” process aimed at optimizing the management of repair stocks. The basic principle of this approach to the replenishment of repair stocks is to function as a centralized worldwide supply chain.
Patrice Daret explains that this concept “brings the idea of forecasts adjusted to real consumption into the equation. Rather than stocking up repair centers on a monthly basis with standard amounts, Thales takes the repair center's consumption into account, and thus supplies the right amounts to the right sites.”
Tangible results
Again, the results have been tangible: “A couple of months on from implementation, Thales is now more agile regarding repair stock flows and the levels of missing parts recorded are better than ever,” according to Patrice Daret. “The level of missing parts has been reduced by 30%. This in turn leads to a better shop processing time with an increase of stock rotation of around 15% and to a better service to our customers.”
Patrice Daret adds that “the benefits for customers will continue to go from strength to strength throughout 2012. Thales will continue to build on these positive results by deploying further improvement initiatives aimed at better satisfying customers.”